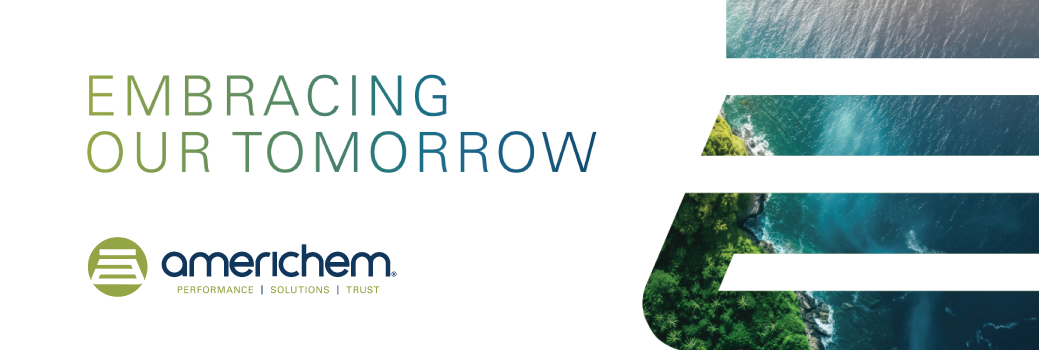
Sustainability At Americhem
In today’s world, operating sustainably is no longer a choice, but a necessity. At Americhem, we recognize that sustainability is fundamental to our future and the well-being of our planet.
Sustainability is a guiding principle that has become a core strategy essential to our business. From the highest level within our organization, we are fully committed to doing our part to better the future, as we believe that sustainability is not just a responsibility, but an opportunity to create a better world for generations to come. We’ve developed sustainability framework built on three critical pillars: People, Process, and Product.
Embracing Our Tomorrow
Read Our Sustainability Report
At Americhem, we are up for the challenge and ready to partner alongside our customers, vendors, and suppliers. Together, let’s work towards a sustainable future for all.
Download Report
Contact Us
Your curiosity can spark change. Please contact us with any questions regarding Americhem's sustainability journey.
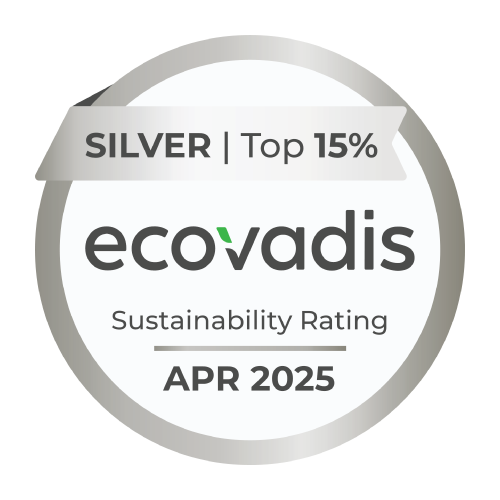
Building Our Sustainable Future: EcoVadis and 2030 Goals
When it comes to sustainability, we are proud of what we’ve accomplished so far, and we are equally as excited about our future ahead.
In 2025, Americhem achieved a Silver-level rating from EcoVadis, a globally recognized assessment platform that rates businesses' sustainability in various categories. This result places Americhem amongst the top 15% of companies assessed by EcoVadis. The EcoVadis rating covers a broad range of non-financial management systems including Environmental, Labor and Human Rights, Ethics, and Sustainable Procurement impacts. View Americhem's EcoVadis Scorecard.
Americhem has established ambitious 2030 Goals that affirm our commitment to progressing our operations, developing sustainable solutions, and empowering our people, all while giving back to the communities in which we operate. Through innovative solutions and strategic partnerships, we aim to deliver sustainable products and services that meet our customers’ evolving needs in a changing world while minimizing our environmental impact.
OUR SUSTAINABILITY STRATEGY
At Americhem, our employees are the cornerstone of our success and the driving force behind our continuous growth. In response to evolving labor markets, demographic shifts, and the rise of digitalization, we are proactive in adapting our strategies to meet these challenges head-on. Our commitment to responsible employment practices is encapsulated in the Americhem Code of Conduct and our Ethics and Human Rights Policy.
Americhem is on a mission to make sustainable manufacturing the new norm. We’re committed to cutting down our environmental impact by getting creative with our resources. Our strategies include reducing waste through lean manufacturing, managing our waste responsibly, boosting energy efficiency, and saving water. With the help of cutting-edge technology and a shift to renewable energy, we’re paving the way toward a greener tomorrow.
Americhem is a global leader in custom color masterbatch, functional additives, engineered compounds, and performance technologies. Our customers demand high-performance materials that are also environmentally responsible. Americhem is dedicated to meeting these challenges head-on by developing innovative products that balance performance with sustainability. We are proud to be a leader in this space and are committed to a greener future.
Americhem’s responsible sourcing strategy is built on a foundation of promoting positive social, ethical, and environmental outcomes throughout our supply chain. We partner with suppliers who adhere to our Supplier Code of Conduct, ensuring ethical practices, employee welfare, and reduced environmental impact. Our commitment to high standards drives meaningful change, influencing every stage from material sourcing to final product delivery.